O-ring Specs & Shelf Life
The O-ring specifications and shelf life for the most common O-ring materials are provided below.
Zero-Leak Gold standard plugs are supplied with the O-ring installed. EPCO can provide any O-ring material that is commercially available, including Buna, Viton, EPDM, Fluorosilicone and AFLAS.
Why are ZLG plug O-rings 70d and SAE 90d? What about the O-ring size relationships—ZLG vs. SAE?
The old style O-ring only SAE port entry plug uses a hard 90d O-ring because the O-ring acts very much like a gasket. During the installation of the plug the O-ring is forced into the taper of the port in an attempt to create the only seal. The cross sectional area of the O-ring is larger than the cross sectional area in which it is installed. During installation the O-ring maybe forced into the threads of port and plug where it can become nibbled. The O-ring may also be extruded from the spot faced area of the port where it can be damaged resulting in a leak path.
The Zero-Leak Gold Plug uses a softer 70d O-ring so the O-ring can respond to the system pressure if the primary seal is compromised. The Zero-Leak Gold O-ring is smaller in cross sectional area than the cross sectional area in which it rests. Under pressure the O-ring acts as a semi-viscous fluid and moves into the leak path to create the second seal. The Zero-Leak Gold Plug O-ring is smaller than its SAE J514 counterpart. All Zero-Leak Gold O-rings are standard metric size O-rings. The O-ring sizes for each ZLGP are listed in the plug/spec sheets next to the corresponding ZLG Plug size.
Standard O-ring Options
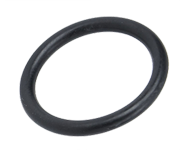
Basic Requirements | Specification | 1255 |
Hardness, points | 70+5 | 71 |
Tensile strength, min, psi | 2031 | 2175 |
Ultimate elongation, min, % | 250 | 258 |
Tear resistance, Kg-cm | – | 46 |
Modulus at 100%, psi | – | 700 |
Modulus at 200%, psi | – | 1784 |
Specific gravity | – | 1.22 |
Additional Requirements | Specification | 1255 |
A14 Heat resistance, Test Method D573, 70h at 100C | ||
Change in hardness, points | – | +2 |
Change in tensile strength, % | – | +4 |
Change in ultimate elongation, % | – | -14 |
Change in volume, % | – | -1.2 |
B14 Compression set, Test Methods D395, Method B, max,%, 22h at 100C | 25 | 8 |
EA14 Water resistance, Test Method D471, 70h at 100C | ||
Change in hardness, points | ±10 | -3 |
Change in tensile strength, % | – | +1 |
Change in ultimate elongation, % | – | -6 |
Change in volume, % | ±15 | +5.4 |
EF11 Fluid resistance, Test Method D471, Reference Fuel A, 70h at 23C | ||
Change in hardness, points | ±10 | -3 |
Change in tensile strength, max, % | -25 | -6 |
Change in ultimate elongation, max, % | -25 | -4 |
Change in volume, % | -5 to +10 | +2.5 |
EF21 Fluid resistance, Test Method D471 | ||
Change in hardness, points | 0 to -30 | -14 |
Change in tensile strength, max, % | -60 | -42 |
Change in ultimate elongation, max, % | -60 | -38 |
Change in volume, % | 0 to +40 | +23.8 |
EO14 Fluid resistance, Test Method D471, No. 1 Oil, 70h at 100C | ||
Change in hardness, points | -5 to +10 | +7 |
Change in tensile strength, max, % | -25 | +10 |
Change in ultimate elongation, max, % | -45 | -12 |
Change in volume, % | -10 to +5 | -9.5 |
EO34 Fluid resistance, Test Method D471, No. 3 Oil, 70h at 100C | ||
Change in hardness, points | -10 to +5 | -2 |
Change in tensile strength, max, % | -45 | +6 |
Change in ultimate elongation, max, % | -45 | -4 |
Change in volume, % | 0 to +25 | +0.8 |
F17 Low-temperature brittleness, Test Methods D2137, Method A, 9.3.2, nonbrittle after 3 min at -40C | pass | pass |
TR10 Retraction at Lower Temperatures (TR Test), ASTM D1329 – 08, Celcius | -29C |
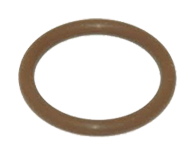
75 Durometer Brown Viton
To meet ASTM D 2000
M2HK710A1-10B38C12EF31EO78Z1Z2
Basic Requirements | Specification | 2988 |
Z1 Hardness, points | 75 + 5 | 76 |
Tensile strength, min, psi | 1450 | 1802 |
Ultimate elongation, min, % | 175 | 193 |
Tear resistance, Kg-cm | – | 24 |
Modulus at 100%, psi | – | 1133 |
Specific gravity | – | 2.168 |
Additional Requirements | Specification | 2988 |
A1-10 Heat resistance, test method D573, 70h at 250C | ||
Change in hardness, max, points | + 10 | + 4 |
Change in tensile strength, max, % | – 25 | – 4 |
Change in ultimate elongation, max, % | – 25 | – 20 |
Change in volume, % | – | – 3 |
B38 Compression set, Test Methods D395, Method B, 22h at 200C, max, % | 50 | 20 |
C12 Resistance to ozone, 50 pphm x 70h at 40C | Pass | Pass |
EF31 Fluid resistance, Test Method D471, Reference Fuel C, 70h at 23C | ||
Change in hardness, points | ± 5 | – 4 |
Change in tensile strength, max, % | – 25 | – 8 |
Change in ultimate elongation, max, % | – 20 | – 17 |
Change in volume, % | 0 to + 10 | + 5 |
EO78 Fluid resistance, Test Method D471, Service Fluid No. 101, 70h at 200C | ||
Change in hardness, points | – 15 to + 5 | -9 |
Change in tensile strength, max, % | – 40 | – 22 |
Change in ultimate elongation, max, % | – 20 | – 18 |
Change in volume, % | 0 to + 5 | + 13 |
EO14 Fluid resistance, Test Method D471, ASTM #7700 Oil, 70h at 200C | ||
Change in hardness, points | – | – 12 |
Change in tensile strength, % | – | – 23 |
Change in ultimate elongation, % | – | – 29 |
Change in volume, % | – | + 17 |
Z2 TR10 Low Temperature Retraction, Test Method D1329, 38.1mm die, 50% elongation, retraction 10% min, Value C degrees | – 16.3 (2.66F) |
O-ring ‘shelf-life’ is the estimated period from the date of cure to the date installed that O-rings will retain physical properties conforming to the specifications. The shelf lives shown below assume normal storage conditions, with minimal exposure to sunlight, ozone, chemicals and extremes of temperature.
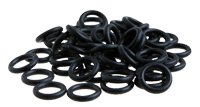
O-ring ‘shelf-life’ is the estimated period from the date of cure to the date installed that O-rings will retain physical properties conforming to the specifications. The shelf lives shown below assume normal storage conditions, with minimal exposure to sunlight, ozone, chemicals and extremes of temperature.
Polymer Name | Chemical Name | Shelf Life (years) |
Aflas | Fluorocarbon Propylene | 20 |
Butyl Rubber | Isoprene/Isobutylene | 10 |
Carboxy Nitrile | Carboxylated Nitrile | 10 |
EPDM | Ethylene/Propylene/Dienne | 10 |
Fluorosilicone | Fluorinated Polysiloxane | 20 |
Hydrin | Epichlorohydrin | 10 |
Hypalon | Chlorosulfonated Polyethylene | 10 |
Natural Rubber | Natural, Hevea | 3 |
Neoprene | Polychloroprene | 10 |
Nitrile | Butadienne/Acrylonitrile | 10 |
Saturated Nitrile | HSN | 10 |
Silicone | Polysiloxane | 20 |
Thiokol | Polysulfide | 20 |
Urethane (ester) | Polyurethane | 5 |
Urethane (ether) | Polyurethane | 10 |
Vamac | Polyetheracrylate | 20 |
Viton / Fluorel | Fluorocarbon | 20 |
Contact us with any inquiries about specific O-ring materials for your Zero-Leak Gold Plug applications.